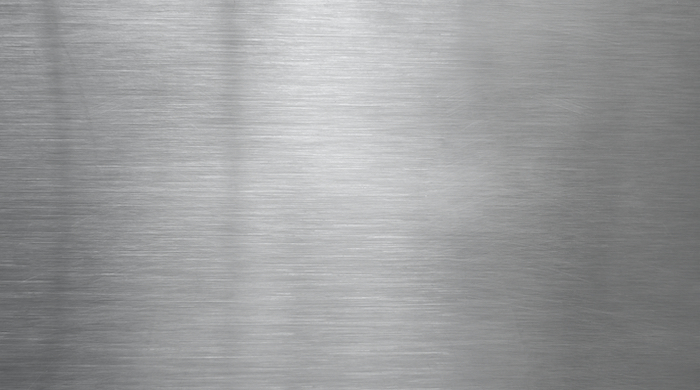
Stainless Steel
Polished stainless steel is one of the most widely used metals throughout the world. With its sheer strength, corrosion resistance, and ability to take on a range of finishes, it’s a highly versatile metal and is broadly available in many compositions.
The alloys detailed below represent a few of the most popular for architectural applications; other alloys are available upon request. At Polished Metals, we work with hundreds of stainless alloys along with polished stainless steel finishes, so please contact us if you have a special requirement and do not see it listed here. Click here for available sheet sizes.
What Is Polished Stainless Steel?
An alloy of iron and carbon, stainless steels typically contain at least 10.5% to 11% chromium along with trace amounts of various other alloying metals that enhance properties such as corrosion resistance, strength, or various other characteristics.
The addition of chromium grants stainless steel much more protection against corrosion compared to basic steel, and stainless steel is frequently used in polished form due to its sheer strength, amenability to various finishes, and appearance.
Stainless steel is broadly used across many industries, including architecture and design, ornamentation, industrial applications such as food and pharmaceutical storage, furniture and countertops, transportation, and more.
Common Stainless Steel Alloys
Rather than a singular form, stainless steel is manufactured using a wide variety of compositions, several which are often seen in polished or finished form across various industries and applications. A few of the most common stainless steel alloys we work with include:
304
This austenitic alloy contains 18% chromium and 8% nickel. It is one of the most widely used alloys because it offers good corrosion resistance and has excellent forming characteristics. 304L is the low carbon version of this alloy and offers better welding and corrosion resistance without the need for post-welding annealing.
304 stainless steel has many general uses as a polished metal, including for elevators, appliances, sculptures, general sheet metal fabrication, furniture, signage, storefronts, entrances, interiors, automotive, solar, refrigeration cases, display cases, and truck parts & accessories.
316
This austenitic alloy contains 16% chromium, 10% nickel, and 2% molybdenum. The combination of higher nickel content and the addition of molybdenum make this much more corrosion resistant than 304. It is commonly used where contact with seawater or brine solutions will be expected. 316L is the low carbon version of this alloy and offers better welding and corrosion resistance without the need for post-welding annealing.
Popular uses for 316 stainless steel include the same as above, though is often used where greater corrosion resistance is needed, including exteriors (particularly in marine environments), marine hardware, and within the pharmaceutical industry.
430
This ferritic alloy contains 16% chromium and no nickel. It is highly magnetic and offers only very basic corrosion resistance, nowhere near as good as the 300 series alloys. It has limited forming and welding characteristics and it can not be hardened by heat treating.
Popular uses for polished 430 stainless steel are similar to 304 stainless steel, but this alloy is available at a lower cost while providing less corrosion resistance.
441
This ferritic alloy contains 18% chromium and has corrosion resistance similar to that of 304 stainless steel. It has good weldability due to titanium and niobium stabilization and has extreme resistance to stress corrosion cracking.
Popular uses for 441 stainless steel include appliances, food and kitchen equipment, heat exchangers, and architectural projects.
Duplex
Duplex stainless steel alloys have a structure that contains both ferrite and austenite. Duplex alloys have higher strength and better stress corrosion cracking resistance than most austenitic alloys and greater toughness than ferritic alloys, especially at low temperatures. The corrosion resistance of duplex alloys depends primarily on their composition, especially the amount of chromium, molybdenum, and nitrogen they contain. Duplex alloys are often divided into three sub-classes: Lean Duplex, Standard Duplex, and Superduplex.